
Written by Rebecca Turley
From Raw Material to Finished Product: The Five Components of Supply Chain Management
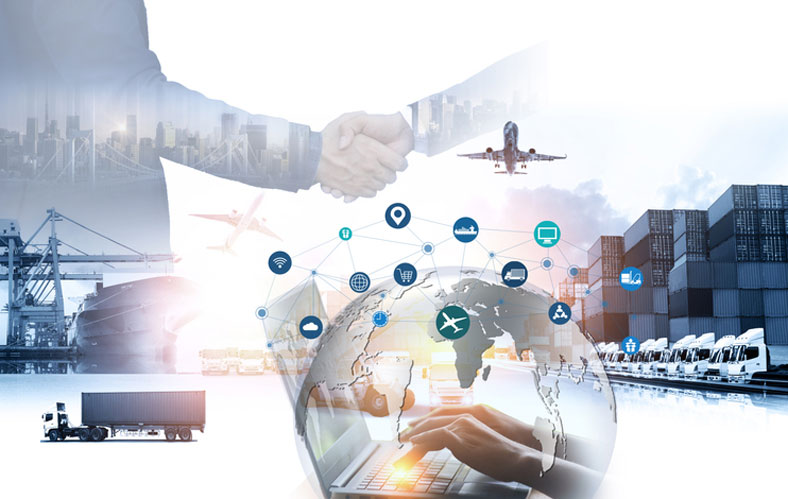
What Are the Five Components of Supply Chain Management? Given the sheer size of today’s global enterprises, it’s easy to envision supply chain management as a highly complex process with tentacles reaching out in every direction to every corner of the globe. But despite all its moving parts, even the most intricate global supply chains can be broken down into five major components – planning and analysis, sourcing, manufacturing, distribution… and in the case of ecommerce giants like Amazon, there’s also returns.
Supply chain management comprises a product’s entire lifecycle. It encompasses all the people, processes, activities, and resources that take a product from a raw material to a finished consumer good. Supply chains are built, maintained, and constantly fine-tuned to minimize risk, streamline the links that connect the process, and gain a competitive advantage in the marketplace.
Companies of every scope and size call on the talents of supply chain managers and leaders to oversee the supply chain management process and ensure that it’s efficient, cost-effective, and resilient. And in today’s global landscape, where supply chain activities occur in all corners of the world, their role has never been more important.
Supply chains can be short, consisting of just a few links that take a collection of domestically sourced raw materials and components through manufacturing to become a market-ready product … Or it can consist of a highly complex network of suppliers and partners, touching hundreds of points around the globe over the course of many months before finally being ready to ship to wholesalers, placed on retail store shelves, or direct to consumers. But in all cases, it can be broken down into these five components:
1. Planning and Analysis
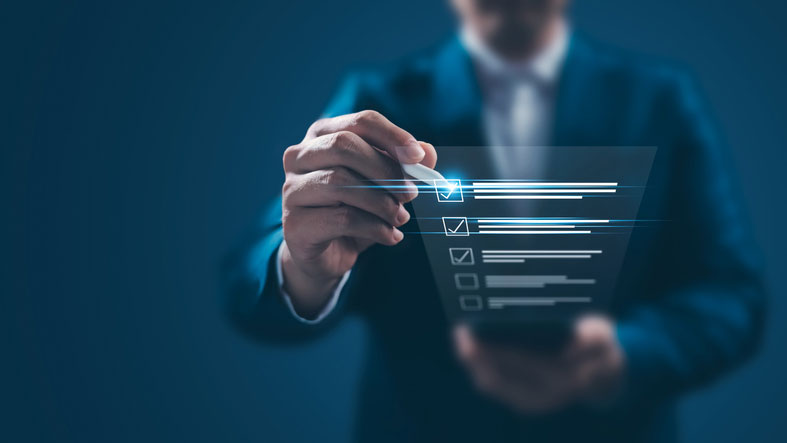
You can’t put a solid plan into motion without proper planning. Supply chain management begins with crafting a thoughtful strategy that’s built around identifying and studying a company’s current and future needs.
A good plan consists of strategies aimed at:
- Negotiating supply and demand
- Assembling and organizing the resources, people, and materials required to meet a company’s needs
- Minimizing operating costs
- Streamlining operations
There are several steps within the planning and analysis component of supply chain management:
-
Demand Planning: The planning process considers supply and demand, with most companies kickstarting the process with demand planning – determining supply and demand based on historical data, projected sales, market conditions, and other factors. The information gleaned through demand planning is passed down to all teams within the supply chain, who then coordinate their efforts to achieve an organizational goal.
Demand planning serves as the foundation off which all other supply chain processes operate. Much of today’s demand planning is accomplished using advanced technologies like AI and machine learning that apply real-time data, historical sales, and market conditions to make accurate predictions. -
Supply Planning: Once supply and demand are determined, supply chain management professionals must begin creating the strategy that will put the plan into motion.
Just a small sampling of the issues considered during the supply planning stage include: What raw materials are needed? Where will the materials be sourced? How and where will manufacturing take place? What equipment is needed to produce the product? Who will provide warehousing and distributing activities, and how will the product make its way to the supplier, retailer, or consumer? - Production Planning: What does the production of the product look like? How will the company produce what is needed without creating an inventory surplus?
- Sales and Operation Planning: During the sales and operations planning stage, the sales and marketing teams come together to ensure their plans match operational objectives.
2. Sourcing (Procurement)
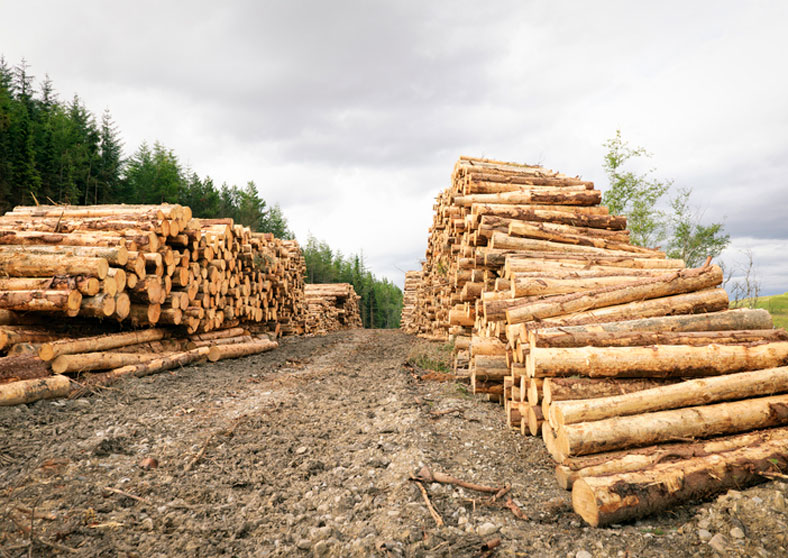
Sourcing is often seen as one of the most critical components of the supply chain management process, as it is where some of the most significant cost savings can be achieved. Sourcing encompasses the entire procurement process, which includes selecting suppliers, ordering, receiving, and managing inventory, and then authorizing supplier payments.
For many companies, the sourcing process is highly complex, with large organizations sometimes working with thousands of suppliers. For example, Starbucks works with some 300,000 coffee growers around the world to source its coffee beans.
Supply chain management professionals identify suppliers that meet a company’s needs and negotiate contracts to receive the necessary goods. They also focus much of their efforts on nurturing supplier relationships and maintaining a diversified network of suppliers to mitigate risks and quickly remediate issues that could affect supply shortages.
For example, a variety of issues in global trade can disrupt the delicate supply/demand balance. Geo-political pressures, tariffs, regulatory barriers, and infrastructure bottlenecks are just some of the challenges associated with importing and exporting across international borders.
Even regional and local issues can create major supply chain backups. For example, a major snowstorm along the eastern seaboard can thwart the movement of goods and severely disrupt a manufacturer’s supply chain. Therefore, manufacturers are always best served by maintaining a network of suppliers in different geographic regions to head issues off at the pass. Supply chain management professionals must be able to pivot their sourcing plans on a moment’s notice to prevent supply chain disruptions.
3. Manufacturing and Production (Operations)
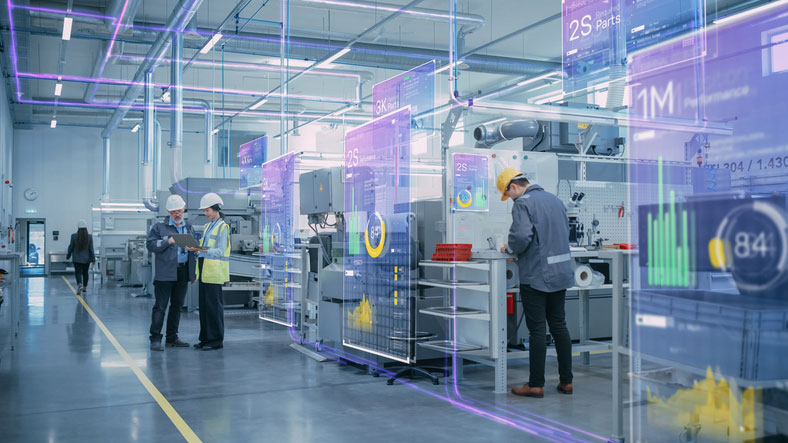
The manufacturing and production component of supply chain management is where the magic happens, when planning and sourcing efforts come to fruition to allow the company to transform raw materials and components into the finished product.
During this central stage of the supply chain process, it’s the responsibility of supply chain management professionals to oversee all activities associated with the in-house production of goods, including product testing, production output, packaging, inventory optimization, and quality assurance. Supply chain managers are also on the lookout for any issues and for opportunities to fine-tune the sourcing or manufacturing process.
4. Distribution (Transportation, Warehousing, & Logistics)
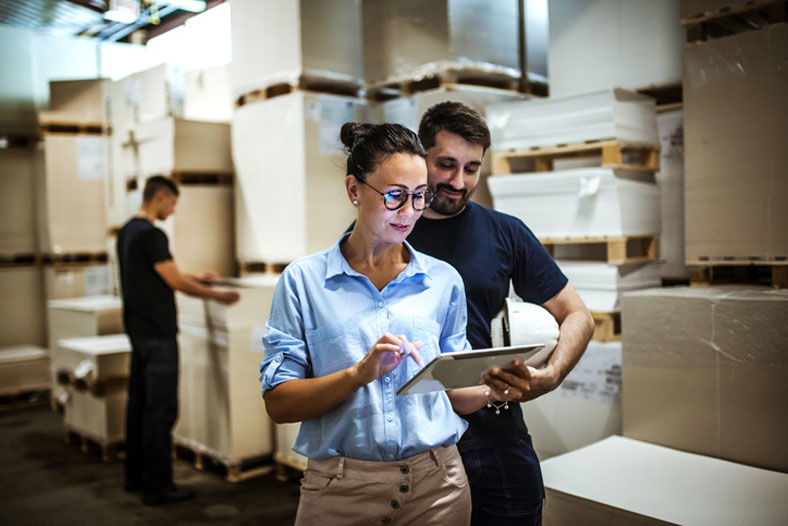
The distribution stage of the supply chain management process encompasses the activities associated with getting the finished product to consumers.
At this stage, supply chain management professionals (1) determine the logistics of how the product will move efficiently to the next step in the supply chain; (2) implement formal distribution plans; and (3) work with distribution partners to move the finished product through one or more distribution channels:
- Direct sales – Manufacturers sell directly to the consumer.
- Wholesale – Wholesalers purchase products in bulk from manufacturers to resell to retailers.
- Brokerage – Manufacturers use brokers to act as middlemen to negotiate sales with retailers.
- Dual distribution – Some manufacturers and vendors employ different distribution channels for getting their products into customers' hands. This could mean B2B sales, selling to wholesalers, and directly to consumers.
The distribution component of supply chain management explores how inventory will make its way into the hands of wholesalers, distributors, and retailers.
Inventory and warehousing management software and leading-edge technologies allow supply chain managers to better plan the distribution process and put plans in motion that make it more resilient and reliable.
5. Returning (Reverse Logistics)
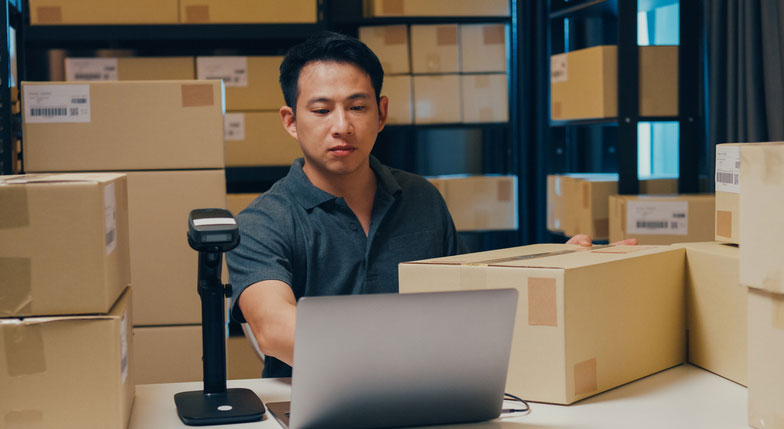
Also often referred to as reverse logistics, the returning component of supply chain management is the process of receiving returned products and the protocol for assigning refunds. Returns may be associated with product recalls, damaged or defective products, or simply consumer dissatisfaction.
This stage has the potential to create a ripple effect throughout the entire supply chain, particularly when dealing with products that don’t meet quality or safety standards. Strong supply chain management leaders during this stage work to identify product issues and coordinate the actions necessary to remediate them.