
Written by Scott Wilson
If you’re going to be working in supply chain management in any kind of large company, you had better get familiar with the tools and terms in use today. ERP and SCM are two of the big ones. You’ll hear them tossed around casually in conversation and see them popping up in papers and articles in logistics trade magazines.
Let’s start with the basics:
- SCM: Supply Chain Management - You already know this one… SCM is the collection of processes that coordinate and optimize a company’s sources for raw materials and components, manufacturing, storage, and distribution from end-to-end.
- ERP: Enterprise Resource Planning - ERP is shorthand for a software platform that is used company-wide to integrate planning and management for more efficient business operations. ERP software often automates certain processes and allows for a common reference point for reporting and information collection.
While SCM is often used to refer to the entire set of tools and processes of supply chain management, ERP refers specifically to a particular software package that is used in the enterprise resource planning process. So, comparing ERP vs SCM really comes down to a side-by-side comparison of ERP vs SCM software.
While supply chain management is a vital and important part of the enterprise resource planning as a concept, it has a more complicated relationship with ERP as a software package.
Enterprise Resource Planning Software Runs the Whole Business
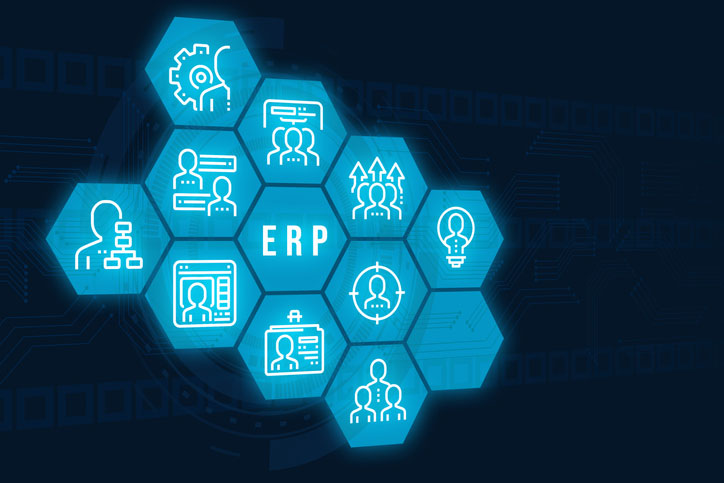
ERP is heavyweight software that comes with a lot of capabilities… and potentially a lot of complications.
Many modern ERP systems are modular. Companies pay for the subsystems they need, such as:
- Accounting
- Sales and Distribution
- Customer Relationship Management
- Human Resources
- Analytics and Reporting
- Customer Service
- Quality Assurance
Most, but not all, ERP vendors have a supply chain management module. There is often a cluster of additional sub-modules within an SCM module, like:
- Planning and Forecasting
- Procurement
- Inventory management
- Fulfillment
Big, mature ERP juggernauts like SAP may even get into the weeds with modules that handle demand forecasting and other esoteric supply chain processes. Other ERP vendors, like QAD, come through with robust SCM applications due to a focus on industries like manufacturing that traditionally need strong supply chain tools.
If an ERP Handling Supply Chain Management Doesn’t Work, neither Does the Supply Chain
As the centerpiece for management and administration, ERP systems take up a lot of oxygen in the corporate IT department. They represent a big investment with a lot of capabilities… and a crucial single point of failure.
Mission Produce’s Supply Chain Operation Found Out the Hard Way When a New ERP System Was Implemented
Although details are sketchy, what emerged in subsequent and slightly embarrassed earnings calls was that the new system resulted in a lack of visibility into inventory on hand. When you are producing avocados, you can’t really take an operational pause to get your numbers right — they are ripe when they are ripe. Both consulting costs and third-party procurement rose while returns spiked.
In fact, the internet is littered with stories of companies that have attempted ERP implementations, spending millions of dollars in the process, only to end up scrapping them as unsuitable in the end. Worse may be those that are completed, but then throw supply chain operations into such chaos that even more money is lost in sales and wastage.
It’s not unheard of for such scenarios to end in lawsuits and recriminations.
ERP and SCM Certification Is a Big Plus for Supply Chain Managers
The importance of supply chain managers capable of mastering ERP/SCM software is clear to companies with so much riding on those systems. That’s why many organizations love to see SCM job candidates who have professional certifications in ERP systems.
Certifications are big in SCM in general. They offer independent, third-party confirmation of skills and knowledge in dozens of specialized fields.
ERP and SCM software are equally specialized. But instead of independent third-party certification agencies, it’s the software vendors themselves that typically offer training and certification. They have every motivation to ensure that candidates know their systems front to back… and that’s exactly the kind of supply chain manager that companies using the software need.
When It Comes to ERP, SCM Isn’t Always Front and Center
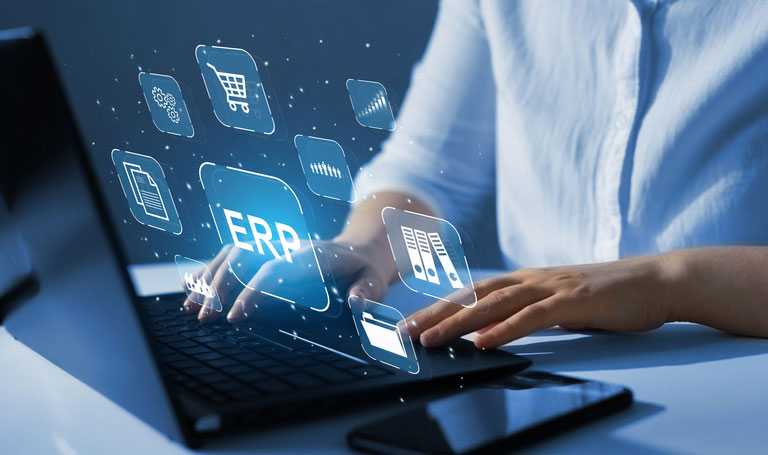
Not all ERP packages offer supply chain management functions… or may only cover some portions of the chain rather than the entire view.
SCM software, on the other hand, is specially designed and optimized for handling supply chain management functions. In fact, most SCM software drills down even further into the stack. You’ll find software packages that focus on transportation, inventory management, load distribution, procurement, and planning.
Of course, the entire point of ERP is to bring all important management functions into one package. So, systems that leave SCM functions out are almost sure to be failures for an enterprise before they even boot up.
On the other hand, consolidation means compromise. An off-the-shelf ERP package will bring with it a particular set of perspectives and relationships between the data it processes. It envisions certain functions performed by certain roles, providing a set of recommendations relating to those functions. But when your SCM organization works to implement those recommendations out in the real world, it’s not uncommon to find roles and functions are either fixed or tough to change.
It’s also true that an ERP SCM module is just a module. In the grand scheme of the developer, it probably hasn’t received as much thought, design, or testing as the core program. It won’t have the features of a dedicated SCM software system.
So, an ERP system handling supply chain management may create some drag on efficiency. In some companies, that’s considered such a detriment that they decide it’s worthwhile to implement a completely separate SCM software system that is better aligned instead.
Interoperability Is the Name of the Game in ERP and Supply Chain Management Systems
These tough choices don’t represent new problems in the ERP/SCM world. Creative companies have long since come up with workarounds to get the best of both worlds.
Like most other types of software today, you can find ERP and SCM packages that are either stand-alone or cloud-based.
Indeed, ERP software providers recognize the obstacles themselves. Many of them cultivate an ecosystem of value-added resellers and consulting firms that have the expertise to customize and assist with implementation projects.
Because big ERP systems are modular and designed for big players, they often have well-defined interfaces and ways to collect and extract data. A major company may have both ERP and SCM software sharing databases and custom functions designed to integrate everything necessary for both logistics teams and senior executives.
When ERP and SCM Work Together, You’ll Never Go Back
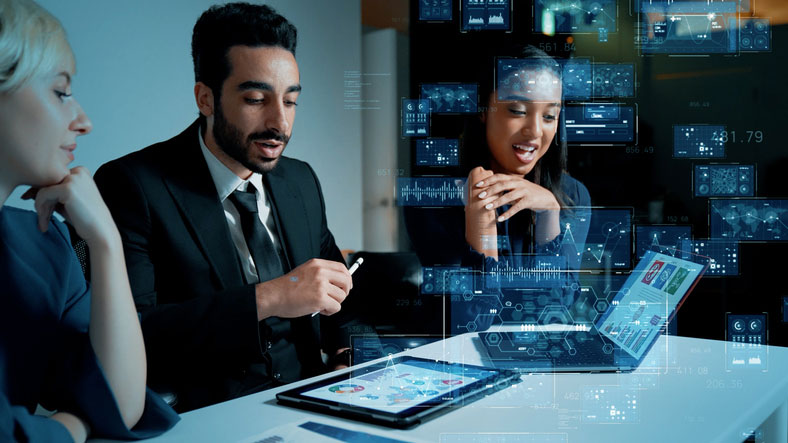
When ERP supply chain management modules are working properly, it’s a thing of beauty. Sales departments enter their projected and actual orders; production calculates their material and capacity needs to meet the demand; procurement immediately starts tapping suppliers to get the raw materials while logistics clears up stock space and arranges transportation for a cycle that can last months.
All that coordination can happen simultaneously. And it can do so in the full view of business leaders, producing detailed reports sent up the executive chain. Seeing a shift in demand or other market trends, they may use it to set strategic changes in motion that will cascade through every department over the course of months or years.
And ancillary functions make use of the supply chain data they get through ERP as well. HR can tell when headcount is likely to ramp up to meet new demands; marketing will have an idea what the impact of their efforts have been and can adjust to fit market realities.
Put it all together and it’s the very picture of what a well-run supply chain in a well-managed business is supposed to look like. Smart supply chain managers will get the education required to master these kinds of technologies fast!