
Written by Rebecca Turley
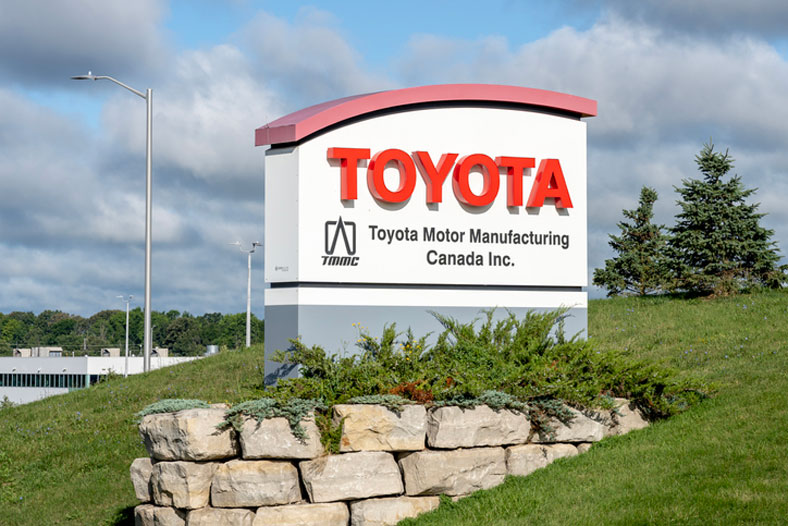
Lean supply chain management is the strategy of eliminating non-value-added time, materials, and resources along every point in the supply chain. In lean supply chain management, the focus is on streamlining the supply chain and eliminating waste. In short, if a step or process doesn’t add to the consumer experience or the bottom line, it won’t make the cut. Reliability and predictability are key, and everything is precisely planned.
Lean supply chain management was originally applied to the manufacturing industry. Toyota is often credited with being the originator of the lean approach, which is why many still refer to it as the Toyota Production System.
Featured Programs:Sponsored School(s)
But today, this approach also encompasses suppliers, vendors, and distribution networks. When a lean supply chain is achieved, the flow of materials and information is streamlined, and cost-effectiveness reigns supreme.
Lean vs. Agile Supply Chain Management Strategies
Lean supply chains aren’t actually built on the concept of flexibility and adaptability. Instead, SCM professionals that employ this strategy are hyper-focused on maximizing the value for the consumer and eliminating waste. Waste can refer to unnecessary production steps, inventory surpluses, transportation delays, material lost in manufacturing, and more.
In lean supply chains, companies prioritize consistency over agility, making it a process well suited for markets where product demand is similarly consistent – things like food and other non-discretionary consumer items. Life cycles for these products are quite long, and there is considerable predictability with little potential for change.
Agile supply chain management is the counterpart to lean supply chain management. Agile supply chains prioritize flexibility. Instead of a lean environment in which inventory levels are prioritized, agile supply chains rely on a competitive environment among suppliers to keep prices low. In this kind of environment, businesses focus their efforts on being nimble enough to slot in different suppliers on the fly. Agile supply chain management is an ideal strategy for products where demand is high for just a short period of time and that can be brought to market quickly. Agile supply chains are also a better option in unpredictable and volatile markets when swift changes in consumer demand require superior adaptability.
Many business models implement both lean and agile supply chain management strategies, working to create supply chains that offer consistency, while still being flexible enough to remain responsive to changes in the market.
How Supply Chain Managers Create Lean Supply Chains Built for Long-term Success
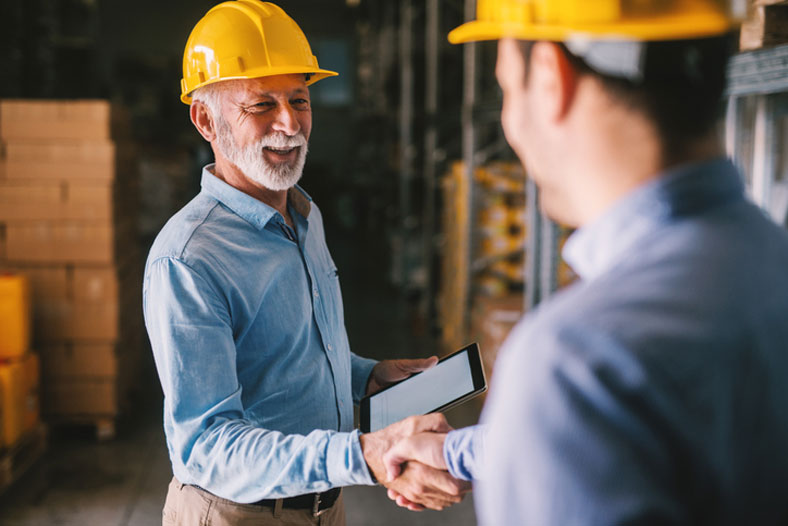
The transition to a lean supply chain can’t be accomplished overnight. Before an organization can get lean, supply chain managers need to establish an environment where it can thrive.
They Develop a Systems Perspective Where Interrelationships Between Supply Chain Partners Thrive
A lean supply chain requires developing the supply chain from a systems perspective—a higher-level, “big picture” perspective that views the supply chain as an interconnected system of companies that never operate in isolation. Here, interrelationships are vital, and partners along the supply chain share techniques and strategies that drive the lean environment from one end of the supply chain to the other. When a systems perspective is implemented, organizations along the supply chain can better achieve their own lean goals.
They Use Value Stream Mapping to Track the Flow of Products and Information to Spot Deficiencies
One of the best ways to kickstart a lean supply chain is to first understand what changes need to be made by mapping the supply chain using a value stream map. Value stream mapping is a workplace efficiency tool that provides supply chain managers with a detailed overview of the supply chain process, from the acquisition of raw materials to the finished product that hits a retailer’s shelves.
Also referred to as value stream analysis or lean process mapping, this tool is essentially a flowchart that breaks down every step in the supply chain process. The concept of value stream mapping was originally created by the Toyota Motor Company (they call it a material and information flow diagram) and is still used by the company today.
A value stream map allows supply chain managers to view the supply chain in its entirety to better understand where products and information are flowing easily and where they’re being bogged down or backed up. Using value stream maps, supply chain management professionals are better able to pinpoint areas of wastefulness and disproportion.
Teams working to produce a lean supply chain begin by creating a current state map, which details the current condition of the supply chain’s material and information flow. They then create a future state map that highlights targeted changes. Multiple maps may be used when considering different plants, customers, or suppliers.
Often, lean supply chain management teams are brought together to create lean value stream maps, updating them to reflect changes in the supply chain or fluctuations in consumer demand.
They Implement Supply Chain Metrics to Keep Both Goods and Information Flowing
Developing a systems perspective includes implementing supply chain metrics – performance indicators that provide companies with insight into the efficiency and productivity of the supply chain.
Metrics in lean supply chain management, which are often focused on inventory management, allow companies to gather information from their trading partners along the supply chain. For example, advanced forecasting allows companies to meet customer demand without overproducing.
When considering the value of implementing metrics in a lean supply chain, companies must ask themselves:
- Does it lower expenses?
- Does it reduce investments in resources?
- Does it sell more products?
Vendor Managed Inventory (VMI), one of the most widely used strategies for inventory management in the consumer goods industry, allows manufacturers to manage their inventory levels based on data provided by retailers and distributors. Through an iron-clad VMI agreement, companies share data using various metrics. Based on the data received, manufacturers generate replenishment purchase orders to keep inventory at an optimum level.
Sony is a good example of a company that changed their supply chain metrics, with the help of their distribution and retail partners, to better monitor the length of time their products were sitting on store shelves. Instead of tracking their “sell-in” sales of products being shipped to stores as completed sales, they began tracking their “sell-through” sales, or those that were purchased and bought from the stores, as completed sales. By considering sell-through sales, Sony was able to better track profitability.
Solutions for the Lean Supply Chain
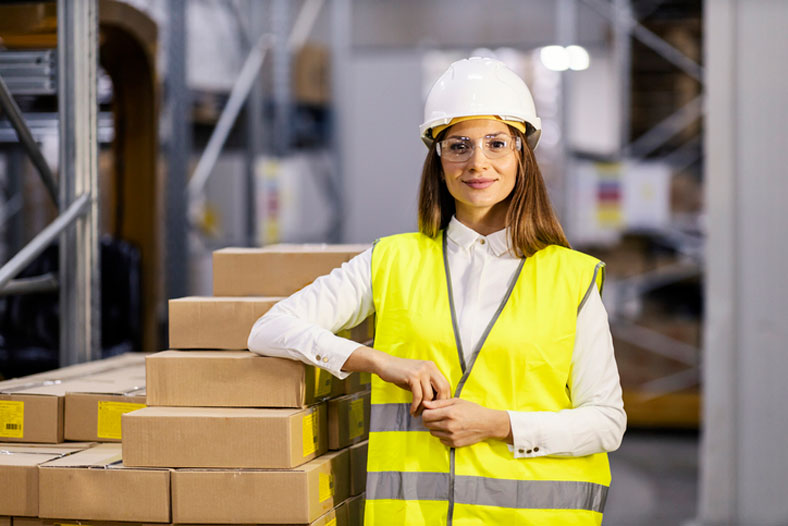
Organizations within a lean supply chain are always looking for ways to reduce waste in the form of:
Excess inventory – Storing excess inventory can become a costly endeavor. Lean companies focus their operations on reducing inventory and minimizing the stock they have on hand. While some degree of inventory is necessary, lean supply chain management is focused on maintaining an emergency reserve and little more.
Untapped employee potential – The best lean supply chains are those in which companies recognize the talents and skills of their employees and use them to fulfill their vision. Failing to recognize the value existing employees bring to the workplace can be a costly oversight.
Manufacturing or packaging waste – Waste from the manufacturing or packaging process can affect a company’s bottom line. Lean supply chains look for ways to reduce waste and create a more efficient manufacturing process.
Poor quality control – Poor quality standards can lead to returned products and product recalls, which result in excess inventory. Setting higher product quality standards leads to fewer returned items, better customer satisfaction, and more sales.
Poor communication – Communication is key in the lean supply chain. An overload of communication or a lack of it can keep important information from hitting its target, whether within a company or along the supply chain. Too much information in the form of multiple channels of communication; a lack of consistency in how messages are delivered; and a lack of opportunities for engagement and feedback are just some of the ways communication can fall flat.